Exploiting a numerical method to translate single tooth bending fatigue results into meshing gears design data: the influence of material properties
Price
Free (open access)
Volume
Volume 10 (2022), Issue 3
Pages
12
Page Range
211 - 223
Paper DOI
10.2495/CMEM-V10-N3-211-223
Copyright
WIT Press
Author(s)
F. Concli, L. Maccioni & L. Fraccaroli
Abstract
According to standards, a fundamental gear design parameter, which heavily influences the sizing of these mechanical components, is the gear tooth root bending strength. To establish this parameter in a reliable way, tests should be performed on running gears (RG) manufactured with the same material and heat treatments under investigation. However, it is common practice in industry and in academia to perform single tooth bending fatigue (STBF) tests, which, on the one hand, are simpler and cheaper to perform, on the other hand, the stress history (cr (t )) they induce is not identical to that obtained during RG meshing. Therefore, it is necessary to apply a correction coefficient (fkorr) to translate data obtained via STBF in RG design data. In recent studies, a method to estimate fkorr through the combination of finite element (FE) simulations and the implementation of multiaxial fatigue criteria (MFC) based on the critical plane concept has been proposed. This method consists of simulating through FE a gear geometry both in the RG load case and in the equivalent STBF condition. Through the load histories recorded on the nodes belonging to the critical area, it is possible, by implementing different MFC, to identify the most critical node and the relative Damage Parameter (DP). The ratio between the obtained critical DP of the STBF case and RG provides the value of fkorr. However, different MFC can lead to different results in terms of fkorr. This is because different MFC differs in the definition of the DP. More specifically, DPs are both functions of material properties, such as the fatigue limit of the material related to symmetric sinusoidal bending stresses (σf) and the fatigue limit at sinusoidal cyclic torsional stresses (τf), and load-dependent characteristics. The goal of this paper is to investigate the effect of different material properties, i.e. σf and τf , on the estimation of fkorr highlighting differences between the various MFC implemented, i.e. Findley, Matake, Papadopoulos, and Susmel et al. To this respect, the above-mentioned numerical method has been applied to a specific gear geometry whose material properties have been systematically varied. Results show that the criteria of Findley and Papadopoulus lead to very similar results and a monotonically increasing relationship between fkorr and τf /σf . A similar trend is observed for the Susmel et al. criterion but with higher value of fkorr Differently, the criterion of Matake leads to a monotonic decreasing relationship between fkorr and τf /σf .
Keywords
Critical plane, FEM, gears, material characterization, multiaxial fatigue, STBF
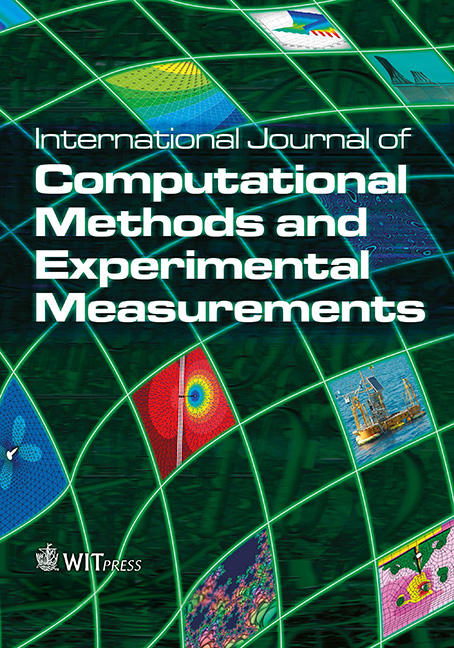