Development of unified framework for microstructure, residual stress, and crack propensity prediction using phase-field simulations
Price
Free (open access)
Volume
Volume 8 (2020), Issue 2
Pages
11
Page Range
111 - 122
Paper DOI
10.2495/CMEM-V8-N2-111-122
Copyright
© 2020 WIT Press, www.witpress.com
Author(s)
Alexander Staroselsky, Ranadip Acharya & Brice Cassenti
Abstract
The approach to obtain a specific user-defined/as-desired or conformal/epitaxial microstructure in additive manufacturing (AM) is a challenging and expensive iterative process. Modeling and validation of solidification microstructure and residual stresses can be leveraged to reduce iteration cost in obtaining as-desired microstructure, minimize residual stress and prevent hot cracking. In the present study, computational fluid dynamics analysis is used to predict melt pool characteristics, and phase-field modeling
is employed to simulate solidification with corresponding microstructure evolution in the as-deposited state for laser powder bed fusion (LPBF) process. Different features of LPBF microstructure such as segregation of secondary elements, dendrite sizes, dendritic orientation and dendritic morphology are
predicted. The methods are further extended to predict orientation change as a function of number of layers. A constitutive materials model coupled to solidification is used to predict the stress in as-built part as well as the effect of stress on microstructural features. The model encompasses the effect of thermo-mechanical and shrinkage stresses and considers creep flow due to the presence of liquid phases in the mushy region. A phase-field-based methodology is proposed that can solve for hot cracking starting
from the intrinsic defects such as porosity in LPBF process. Depending on the residual stress, crack propagation can be predicted from the unified model. The model was incorporated in a finite element code and used to predict crack growth phenomena such as values of critical stress, crack path, etc.
Phase-field models of crack growth reduce the computational complications associated with singularities and allow finite element predictions of crack propagation without remeshing. This work intends to develop a unified phase-field framework that can sequentially predict solidification microstructure, residual stresses and structural cracking.
Keywords
additive manufacturing, crack propagation, microstructure, phase field, residual stress, solidification
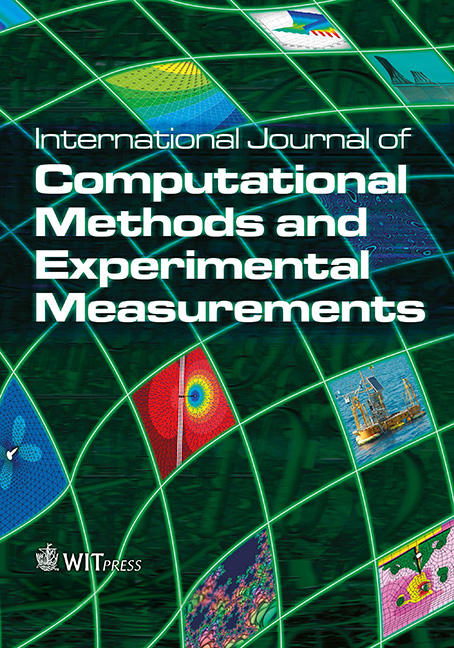