Complex composite structures with integrated piezoelectric transducers
Price
Free (open access)
Volume
Volume 5 (2017), Issue 2
Pages
9
Page Range
125 - 134
Paper DOI
10.2495/CMEM-V5-N2-125-134
Copyright
WIT Press
Author(s)
XIANLONG CHEN, RÉMY LACHAT, SÉBASTIEN SALMON, MORVAN OUISSE & YANN MEYER
Abstract
Nowadays, in different industrial fields as transport or aerospace, a research effort is conducted to reduce the structural weight. One of the most promising solutions is the use of composite structures due to their high stiffness, their low mass density and their low damping factor. At the same time, there is an intensification of the operational dynamic environment and an increase of durability requirements. These different expectations seem to be contradictory. One solution to manage these points is to design and manufacture smart composite structures with a fully distributed set of integrated piezoelectric transducers. These structures are able to modify their mechanical properties with respect to their environment (e.g. active vibration control), to interact with other structures (e.g. mechatronic) or with human beings (e.g. Human–Machine Interaction).
To meet the technical specifications of smart composite structures, in particular for complex geometries, it is necessary to master the manufacturing process and consequently the material parameters of the manufactured composite. Indeed, during the design phase, these parameters have to be absolutely known. A design approach based on engineering system theory and uncertainty calculation is applied to our manufacturing process of smart composite structures. In this paper, two different material identification methods (the Resonalyser technique and the Time-of-Flight technique) were selected and are applied to several test plates and, finally, on a large smart spherical cap. The Resonalyser technique is a good method to extract overall material parameters. Its major drawback in terms of cost and difficulty of implementation is the use of contactless devices for the measurements. The Time-of-Flight technique is based on the duration measurements of pulse propagation with a simple and low cost experimental setup. Integrated piezoelectric transducers are used for this purpose in the present analysis. The results obtained are quite local (mean values along the propagation path) and need a strong physical interpretation. The different material parameters obtained are compared and discussed.
Keywords
complex structure, composite structure, material characterization, transducers integration.
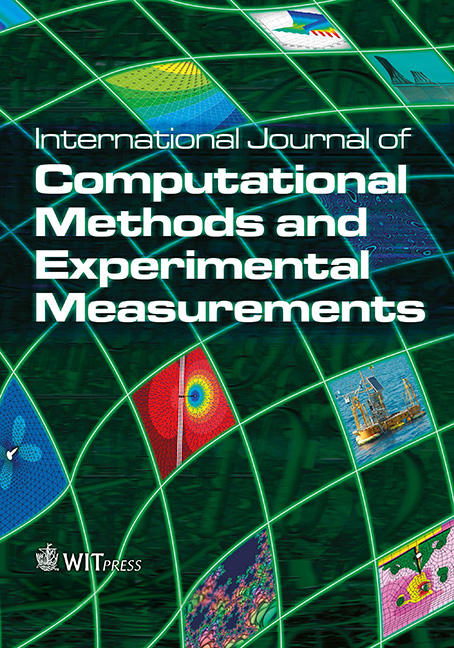